Recently, automation has emerged as a game-changer in a diverse range of manufacturing processes, and plastic injection molding services are part of this evolution. As sectors continue to progress, the incorporation of advanced technologies is enhancing operations, improving precision, and increasing efficiency. The relevance of automation in plastic injection molding is increasingly vital as manufacturers seek to maintain a competitive advantage while meeting the requirements for higher quality and faster production cycles.
As the landscape of manufacturing transforms, the gains of automated solutions in the field of injection molding become increasingly obvious. With the capability to minimize human error, reduce cycle times, and maximize resource utilization, automated systems is changing how plastic products are designed and assembled. In this piece, we will investigate the multiple ways automation is influencing the future of services related to plastic injection molding, and how these developments are setting new standards for quality and efficiency in the sector.
The Rise of Automation in Injection Molding
The field of plastic injection molding service is experiencing a transformation with the rise of automated manufacturing. Manufacturers are more and more adopting automated systems to optimize operations, enhance precision, and cut production costs. With the integration of robots and advanced control systems, companies in this sector can achieve accelerated cycle times and improved product quality. Automation not only boosts productivity but also minimizes the risks linked to human error, making it a essential component of contemporary manufacturing processes.
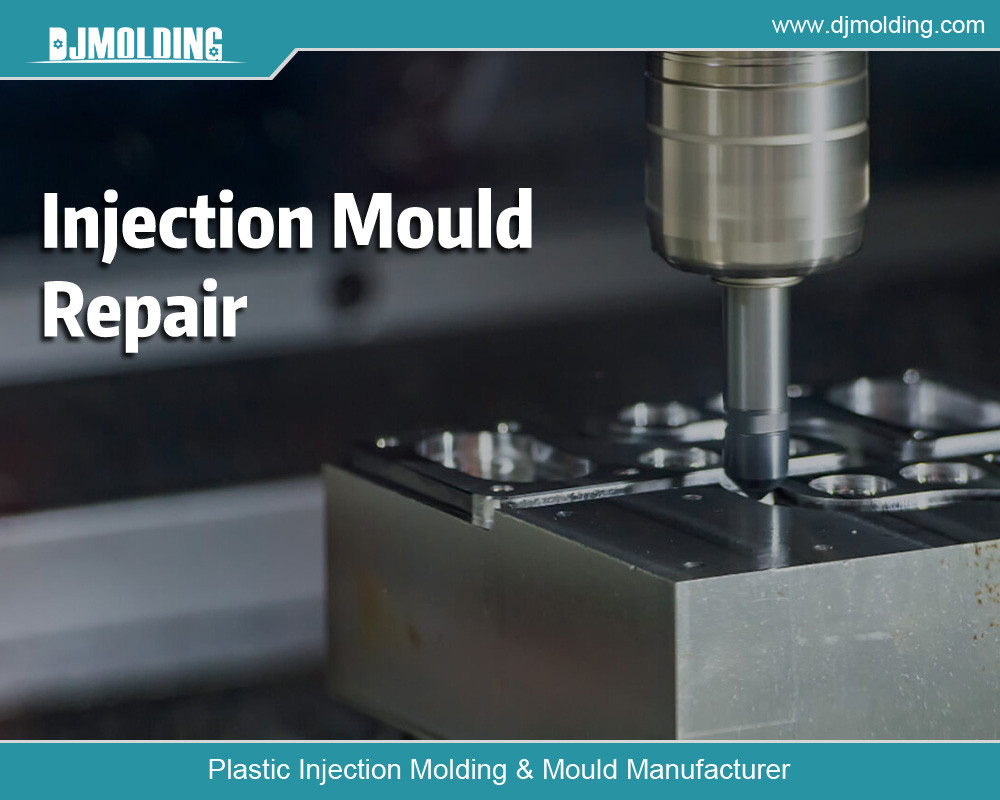
As automated machinery becomes more complex, the abilities of plastic molding services expand considerably. Robotic machines can execute complex tasks, including precise molding, with remarkable speed and accuracy. This feature allows companies to create intricate designs and meet higher customization demands. Additionally, real-time monitoring systems provide immediate data on production metrics, allowing better decision-making and performance optimization.
The growing trend towards automation in injection molding is also influenced by economic factors. As employee costs rise and the need for cost efficiency intensifies, businesses are driven to look for ways to enhance productivity without compromising quality. Adopting automation offers a return on investment through reduced labor costs and improved throughput. As a result, the prospects of plastic injection molding service will likely be marked by increasingly automated processes that deliver superior productivity and advancements in product development.
Perks of Automated Injection Molding Solutions
Automated injection molding services offer increased efficiency which can substantially boost production capabilities. By utilizing advanced machinery and robotics, these services can operate continuously with minimal downtime. This automation optimizes the entire manufacturing process, allowing for more rapid cycle times and a larger output of high-quality plastic components. As a result, businesses can meet greater demand without compromising on quality, resulting in leading to enhanced profitability.
Another key benefit is the uniformity and precision that automation provides. Human error is reduced, and the machines consistently produce parts that adhere to precise specifications. This reliability is critical in industries where precision is paramount, such as the aerospace sector and healthcare devices. With automated systems, companies can achieve narrower tolerances and maintain high-quality standards, which can lead to better customer relationships and a better reputation in the market.
Lastly, automated injection molding services contribute to decreased labor costs. By replacing manual labor with machines and automated processes, businesses can significantly cut on workforce expenses. This change allows companies to redistribute human resources to more value-added tasks, such as design and innovation. Consequently, automation not only drives down production costs but also allows organizations to focus on areas that contribute to long-term growth and development.
Upcoming Trends in Plastic Molding Automation Technologies
As tech continues to evolve, the future of injection molding services services is ready to become highly automatically controlled. One of the most important developments is the integration of advanced automation technology in the production workflow. These robots can handle complex tasks such as material handling, transfer of parts, and quality inspection with incredible accuracy and efficiency. This not only boosts the effectiveness of production but also reduces mistakes made by humans, which contributes to improved product quality and consistency.
Another notable trend is the implementation of AI and ML in the injection molding method. These advancements allow for immediate monitoring and evaluation of production data, enabling manufacturers to improve their processes dynamically. By predicting machine failures and maintenance needs in advance, companies can minimize downtime and maintenance costs while boosting their overall productivity. This intelligent automation promises that plastic injection molding services stay relevant in a fast-paced market.
Lastly, the growth of the Fourth Industrial Revolution and the IoT is positioned to transform how injection molding companies operate. Integrated machinery will facilitate smooth communication among devices and systems, resulting in a more clear and flexible manufacturing system. Data collected from multiple sources will enable companies to make knowledgeable decisions and adapt swiftly to changing market demands. This interconnected approach promises to enhance the efficiency of supply chains and further streamline the production of top-quality plastic parts.